What are the process flow of bio-organic fertilizer disc granulation
Bioorganic fertilizer is a kind of microbial fertilizer produced by modern biological fermentation technology. Bio-organic fertilizer is a kind of pollution-free and pollution-free fertilizer, which is processed by using organic matter of high-quality fertilizer as carrier, adding microbial active bacteria, a small amount of inorganic nutrients and trace elements, and using the equipment of organic fertilizer production line. The process of producing bio-organic fertilizer by disc granulator has its unique raw materials and production process requirements. The fertilizer production line needs fermentation, crushing, mixing, granulation and drying of raw materials.
The process flow of bio-organic fertilizer granulation production line is mainly raw material fermentation, compost crushing, ingredient mixing, disc granulation, rotary drying, rotary cooling, primary screening, secondary screening, metering packaging.
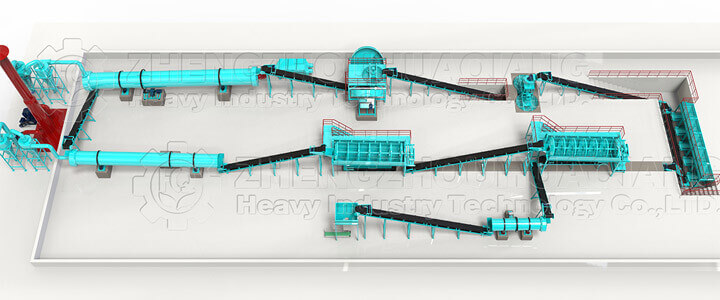
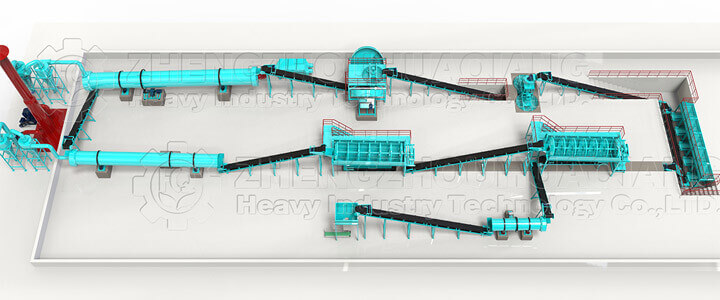
Raw material processing
The raw materials for bio-organic fertilizer fermentation are chicken manure, cow manure, pig manure, straw, soybean meal, mushroom residue, peat and so on. After the raw materials are put into the fermentation tank, the materials need to be turned over to ensure the aerobic fermentation of the materials. The fermented materials need to be crushed. The semi-wet material crusher also has a good crushing effect on the hard-to-grind materials. It can crush the fermented materials into the required size.
Batching and mixing
Additives containing microbial active bacteria and other nutrients were added according to the formulation. Mixing the organic matter and the ingredients, and mixing the materials to meet the requirements of the granulation process.
Granulation operation of disc fertilizer granulator
In the granulating process of organic fertilizer disc granulation production line, the operator should pay attention to the change of granulation water content and particle size, and then adjust the water adding amount and water adding position of disc granulator in time. Water feeding for disc pelletizing should ensure that the quantity of pellets produced is in harmony with the growth rate of pellets, otherwise the particle size fluctuation will occur.
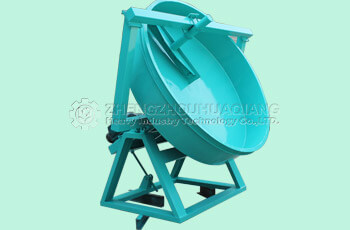
When the pellet production speed is too fast, the material used for pellet growth is insufficient, and the size of the pellet is discharged out of the plate if the size of the pellet does not meet the requirements, and the size of the fertilizer pellet becomes smaller. If the production speed of pellets is too slow, the size of pellets will increase. In order to ensure proper particle size and stable feeding speed, operators should pay attention to production changes and adjust in time. When the water content in the disc is low, the grain size becomes smaller, so the water supply should be increased in time, and vice versa, the water supply should be reduced.
Screening process of organic fertilizer production
After drying and cooling, the organic fertilizer particles enter the screening machine, and the powder is separated from the particles, and the separated powder is re-granulated into the granulating system. Secondary screening separates the qualified product particles from the large particles, and the particles are returned to the disc granulation production line, and then granulated again after crushing.
评论
发表评论